The National Carbon Capture Center (NCCC) is set to host testing of SRI’s promising new carbon capture technology.
SRI is developing a novel mixed salt process (MSP) technology with support from the Office of Fossil Energy and Carbon Management, energy technology company Baker Hughes and the National Energy Technology Laboratory. Pilot bay, engineering-scale testing of the 0.5-megawatt MSP CO2 capture technology is slated to begin at the NCCC in early 2025.
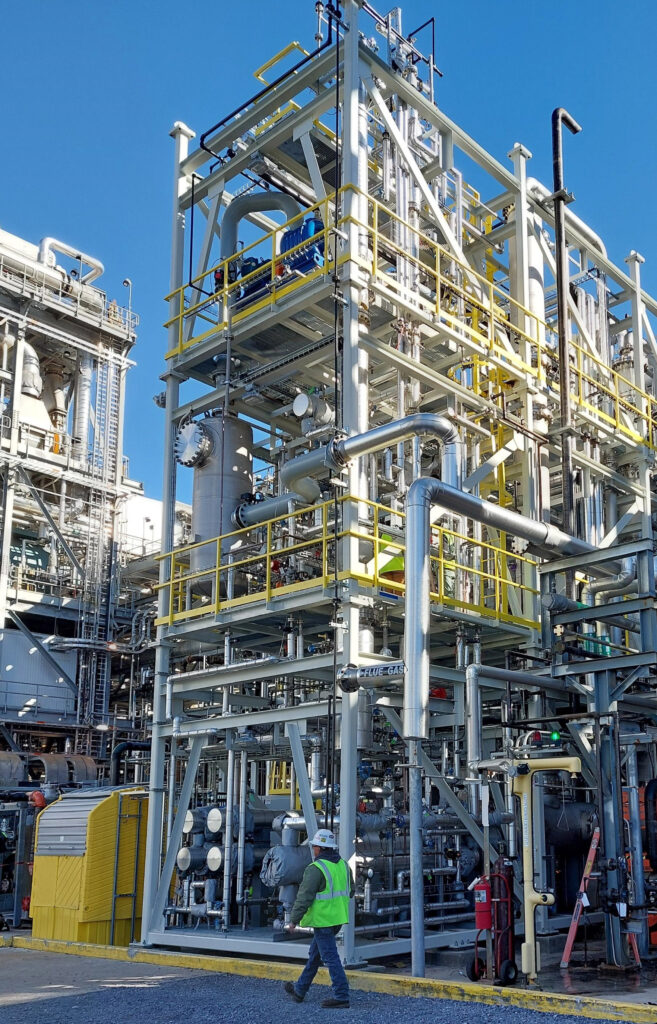
A team effort
The team developing, testing and deploying the MSP technology includes SRI (overall project management), Baker Hughes (cost-sharing industry partner who entered into a global exclusive licensing agreement with SRI for MSP use in post-combustion CO₂ capture), the NCCC (host-site, flue gas and utilities provider, and skid installation/removal), EPIC Systems (modular MSP system fabricator), Trimeric Corporation (process engineering and techno-economic analysis) and OLI Systems (flowsheet modeling).
A brief technology explanation
SRI’s MSP uses an aqueous solvent of environmentally friendly inorganic chemicals to remove CO2 from flue gases of power plants and industrial applications. The process generates pure, pressurized CO2 for sequestration or chemical industry use. Simply stated, the MSP technology combines the strengths of two chemicals – ammonium and potassium carbonate salts – while avoiding their drawbacks. Both chemicals are inexpensive and readily available compared to other advanced solvent technologies.
The MSP works like conventional amine-based solvents in that CO2 is absorbed into solvents in the absorber at ambient pressure and temperature, with very low emissions. However, the solvent is thermally regenerated in a regenerator, providing a pressurized CO2 product. Additionally, MSP uses a two-absorber configuration: the first with a higher ammonia salt concentration, and the second with a higher potassium salt concentration.
Solvent testing preparations
SRI’s four modular skids were delivered and installed in the NCCC pilot bay area last year, to perform engineering-scale MSP demonstration of 5 to 10 tonnes per day of CO₂ capture from coal flue gas and 3.6 tonnes per day from natural gas flue gas.
NCCC’s preparations have included engineering, designing and installing the foundation and suppling flue gas, steam, demineralized water, nitrogen and instrument air to the skid boundary.
Testing on flue gas is expected to begin in early 2025 and will conclude by August 2025.
“The NCCC offers all the necessary facilities for technology developers, including various test bays for both small-scale and large-scale pilot testing,” said Indira Jayaweera PhD, director, carbon and water Management, SRI. “Additionally, the NCCC has a skilled support staff to assist with plant installation and tie-ins with utilities and flue gas. SRI has successfully completed several field-testing projects at the center in the past.”
Future challenges and opportunities
A major challenge for the research and development team is optimizing the MSP process and performance in this integrated and scaled-up design based on the combined salts of two commercially used solvents.
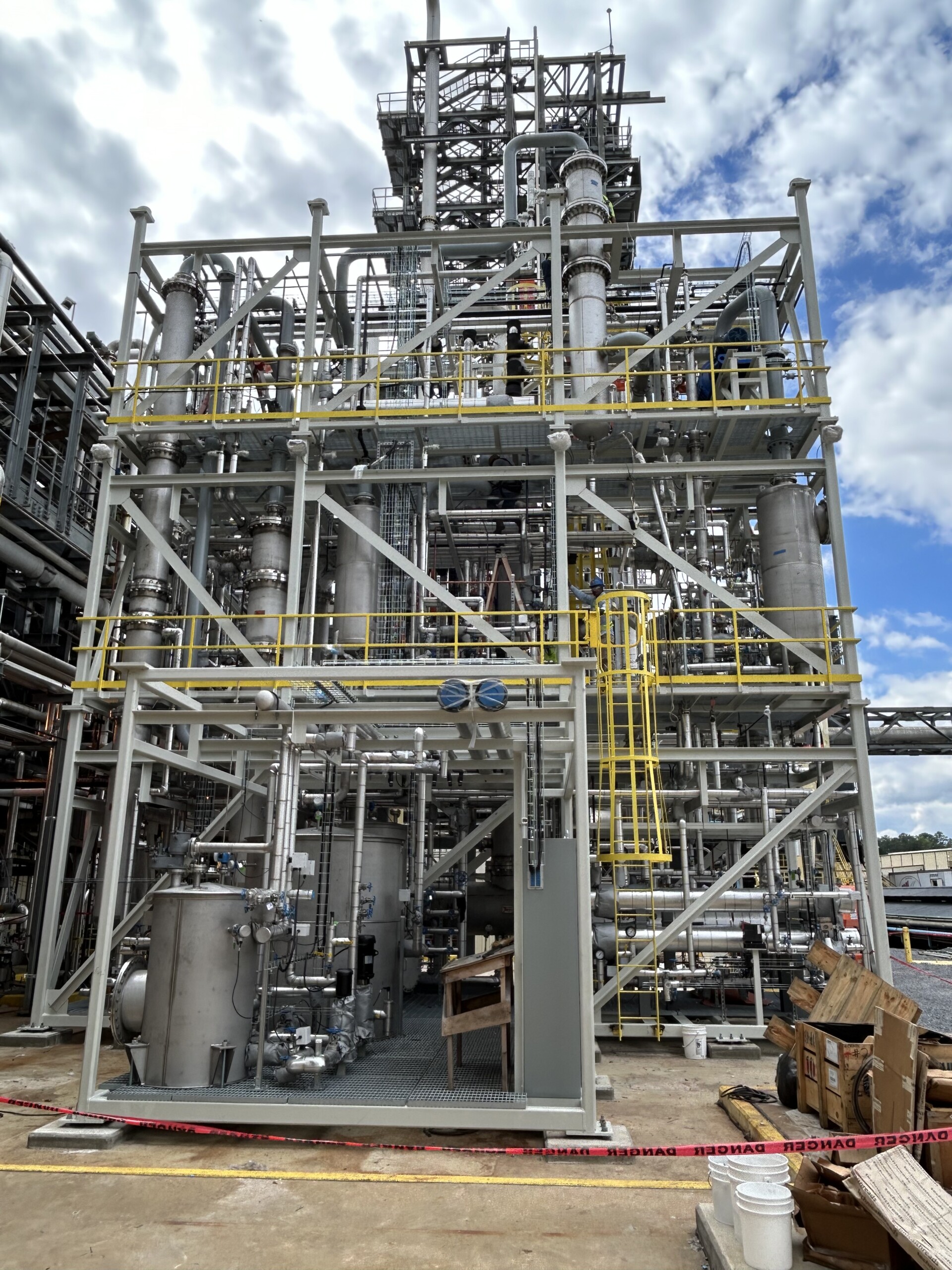
A successful test campaign will demonstrate this technology’s low emission, low energy and high CO₂ loading. The testing should reveal additional improvements needed before scale-up toward commercialization.
“We are pleased that the pilot campaign of SRI’s MSP technology at the National Carbon Capture Center is progressing,” said Daniela Abate, vice president CCUS, climate technology solutions at Baker Hughes. “We believe that the campaign will further document the technology’s potential to contribute to the advancement of CCUS, providing a lower-cost and energy-efficient carbon capture solution.”
Like prior solvent tests conducted at the NCCC, real-world experiences and immense data from the test campaigns will aid technology developers. Lessons learned will improve the solvent formulas, fine-tune the capture process and update models for performance prediction. All these refinements are essential for the technology to scale confidently toward commercial deployment.
The National Carbon Capture Center, managed by Southern Company and funded by the Department of Energy and multiple sponsors, is recognized worldwide for accelerating the development of technologies to reduce greenhouse gas emissions. The NCCC’s highly specialized team advances emerging technologies for deployment, assists in moving technologies to scale-up and then helps usher the technologies to successful commercial deployment.